Ситуация до начала работы
Клиент обратился с запросом на создание системы контроля загрязнения масла в электростатическом маслоочистителе. Задача заключалась в разработке решения, которое в реальном времени измеряет количество и размер частиц примесей в очищаемом масле, а также фиксирует динамику их изменения в процессе фильтрации.
На момент обращения не существовало мобильной системы, способной проводить столь точные измерения на местах диагностики, что затрудняло оперативный контроль чистоты масла в полевых условиях.
Обсуждение вводных
На старте проекта были определены ключевые требования:
● Высокая чувствительность системы к частицам примеси.
● Мобильность устройства, позволяющая оперативное подключение к масляным системам.
● Реализация подсчета частиц с оценкой их размеров.
● Возможность интеграции с ПК для записи данных и последующего анализа.
Клиентом была предоставлена информация о рабочих условиях, параметрах потока масла и допустимых уровнях загрязнения, что позволило сформировать детальный технический запрос.
Технический анализ
После анализа вводных мы выбрали оптический принцип измерений, основанный на регистрации рассеянного лазерного излучения. Принцип работы системы регистрации основан на детектировании рассеянного излучения при прохождении лазерного луча сквозь поток жидкости как на рис. 1.
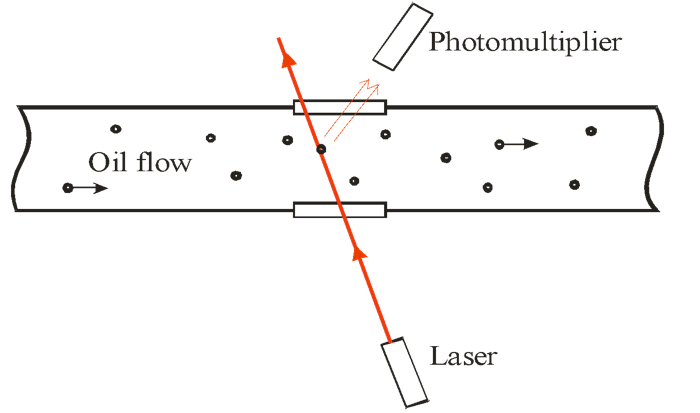
Рис.1. Принципиальная схема работы системы регистрации количества примеси.
Ключевые элементы системы:
● Лазерные модули (5 мВт) с коллиматорной диафрагмой для уменьшения шума и повышения чувствительности.
● Оптические окна для ввода и вывода луча в поток масла.
● Фотодетектор для регистрации отраженных сигналов.
● Микрообъективы для фокусировки отраженного сигнала и передачи его через оптоволокно.
Особое внимание было уделено расчету зоны регистрации частиц, что позволило обеспечить точное соответствие между количеством импульсов фотодетектора и концентрацией примесей в масле.
На рисунке 2 представлены фотографии одного из модулей системы диагностики.
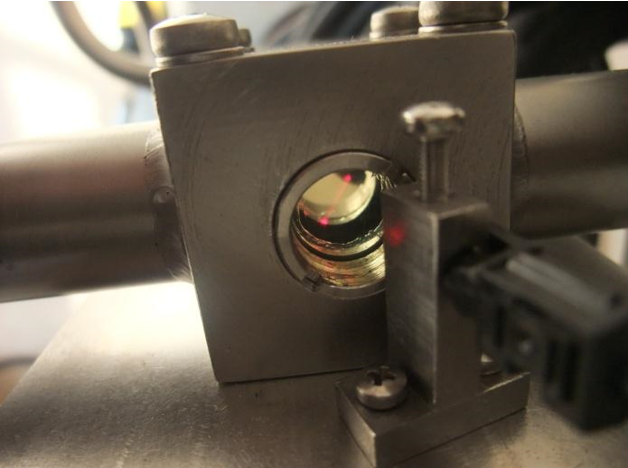
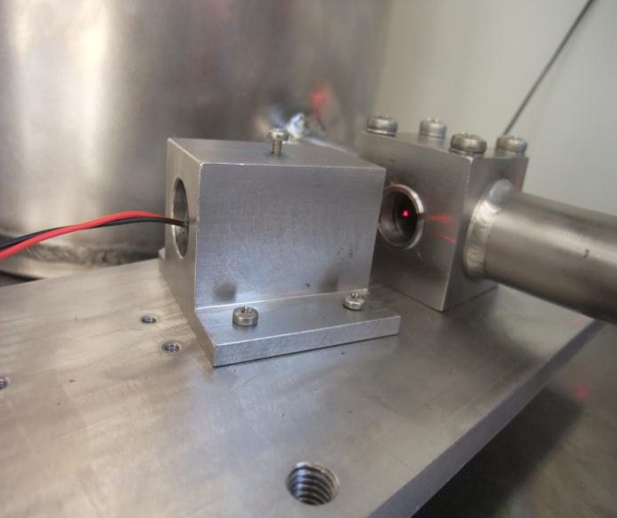
Рис.2. Модуль проточной системы диагностики количества примеси в масле. На левой фотографии виден след лазерного луча в потоке масла.
На рисунке 3 представлены пробы масла с добавлением мелкодисперсного углерода и масло после очистки от этой примеси. В последующей таблице – результаты анализа размеров примеси в пробах.
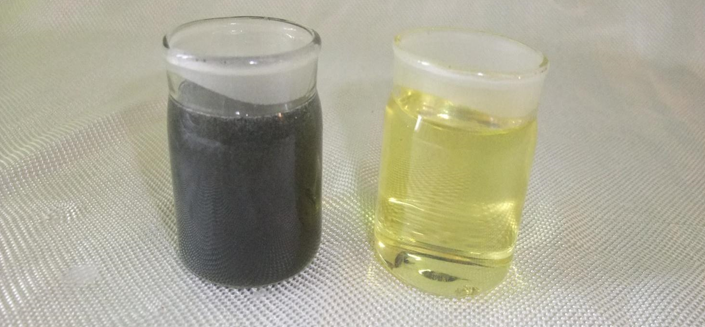
Рис. 3. Проба масла с добавлением углеродной № 3 примеси и масло после очистки № 6.
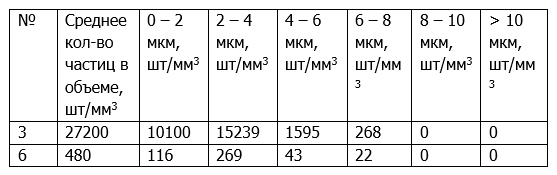
На рисунке 4 представлены пробы масла с добавлением корунда и проба после очистки, в таблице – результат подсчета количества примеси для этих проб.
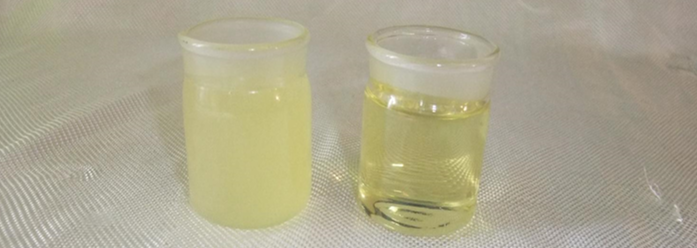
Рис. 4. Проба масла с добавлением корунда № 8, и проба № 10 после очистки.
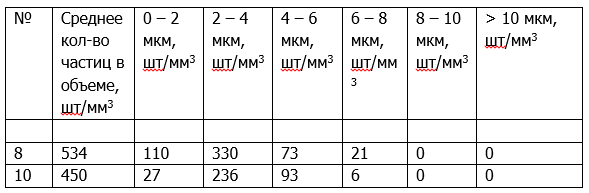
Для обеспечения возможности мобильного контроля загрязнения масла была создана проточная система диагностики, подключаемая к диагностируемым точкам через быстросъемные соединения.
Ключевые аспекты системы:
1. Принцип работы:
○ Лазерный луч направляется через поток масла с помощью оптических окон.
○ Отраженные от частиц примеси сигналы улавливаются микрообъективом и передаются на фотодетектор через оптоволоконный кабель.
2. Методы измерения:
○ Оценка среднего уровня рассеянного света для определения общей прозрачности масла.
○ Подсчет количества частиц по пяти уровням отсечки, что позволяет классифицировать их по размерам.
3. Математическая модель:
○ Рассчитано, что концентрация частиц в зоне регистрации (0.01 мм³) обеспечивает точное определение количества примесей даже для высокозагрязненного масла.
○ Утверждено предположение: каждый импульс соответствует одной частице, если длительность импульса не превышает 100 мкс. Более длинные импульсы рассматриваются как пересечение нескольких частиц.
4. Программная реализация:
○ Сигналы, полученные фотодетектором, обрабатываются микроконтроллером в режиме реального времени.
○ Данные фиксируются с дискретностью 1 раз в 3 секунды и передаются на ПК через специализированное ПО, которое:
- Отображает текущий уровень загрязнения.
- Записывает динамику процессов, включая время регистрации, что позволяет проводить аналитические исследования.
Решение сложных моментов
В процессе разработки мы столкнулись с рядом технических вызовов:
● Шум в сигнале: Паразитные засветки и отражения от оптических окон снижали точность измерений. Для решения была добавлена коллиматорная диафрагма на лазерных модулях, что улучшило отношение сигнал/шум.
● Высокая концентрация частиц: В условиях грязного масла важно было избежать погрешностей из-за пересечения нескольких частиц. Алгоритмы микроконтроллера были адаптированы для учета импульсов с большей длительностью.
Решение задачи
В результате разработки была создана компактная, высокоточная мобильная система диагностики, отвечающая всем требованиям клиента. Ее основные функции:
● Контроль среднего уровня рассеянного сигнала для оценки прозрачности масла.
● Подсчет количества частиц примеси с делением на пять уровней размеров.
● Вывод результатов на дисплей и передача их в ПК для записи и анализа.
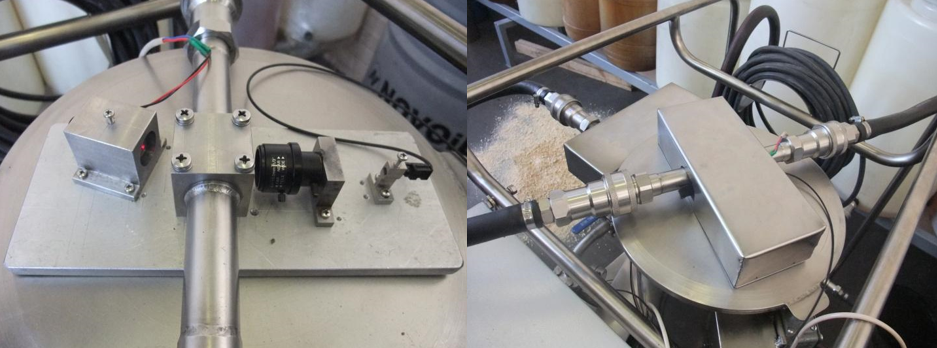
Рис. 5. Оптический модуль мобильной системы диагностики
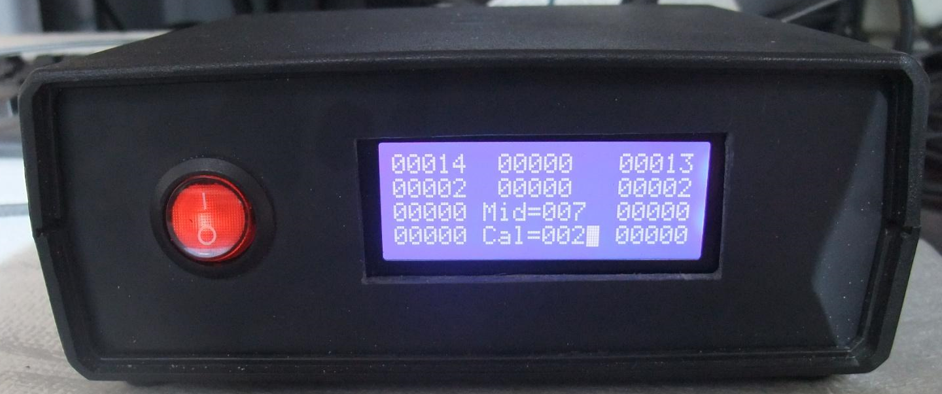
Рис. 6. Передняя панель электронного блока диагностики
На рисунке 6 приведена фотография электронного блока мобильной диагностики со стороны передней панели. Высвечивается реальное количество импульсов по пяти уровням, пересчитанное «эффективное» количество, если длительность импульса превышает 100 мкс и средний уровень рассеяния.
Для записи данных в персональный компьютер была разработана и создана специализированная программа, внешний вид рабочей панели которой представлен на рисунке 7. Помимо самих, поступаемых с микроконтроллера, данных программа позволяет записывать текущее время регистрации, что в последующем позволяет оценивать динамику регистрируемых процессов.
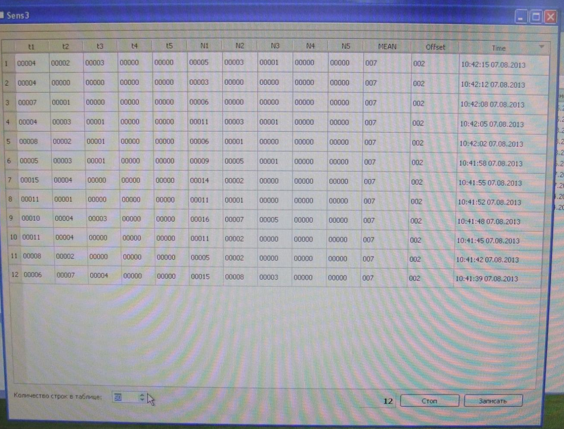
Рис. 7. Интерфейс программы отображения и записи данных
Устройство доказало свою эффективность при тестировании в реальных условиях. Его высокая точность и мобильность обеспечили возможность контроля чистоты масла на любом этапе эксплуатации оборудования.
Заключение
Этот проект стал успешным примером контрактной разработки электроники, сочетающей высокую техническую сложность и практическую пользу для бизнеса. Созданная система помогает клиенту оперативно контролировать качество масла, снижая риски выхода оборудования из строя и минимизируя затраты на обслуживание.
Оптические системы контроля, разработанные нашей командой, показали свою надежность и точность, что делает их востребованным решением в задачах диагностики и мониторинга в различных отраслях